Cheap Becomes Expensive in Product Manufacturing
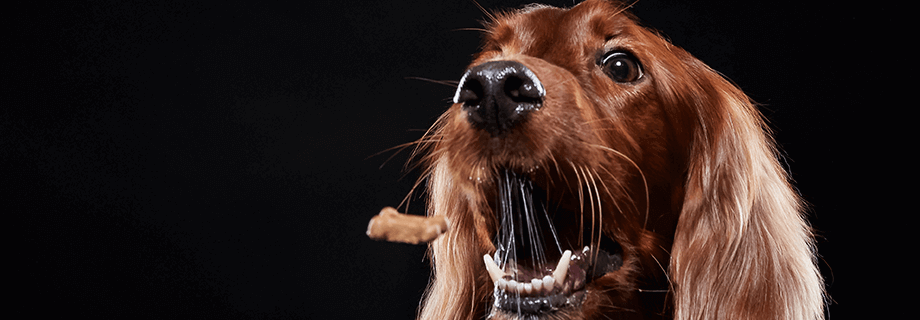
Occasionally, we get into a discussion with small extrusion business owners who seek our advice on using proper nutritional requirements and typical ingredients to be used to manufacture quality products, as well as other operational parameters.
After discussing with these customers, many will stick to the recommendations, while a few will not. Those who don’t follow the recommendations may start modifying the formula or the recipe to include a cheaper ingredient at much higher inclusion rate than recommended, as long as they can manage to extrude and shape the kibble or meet the protein guarantee on the tag.
The reason nutritionists suggest certain ingredients and proportions is based on the known nutrient requirements for a given species, age/growth phase, environmental management conditions, and defined objectives.
Animals utilize nutrients supplied by the ingredients in the recipe to meet their need for maintenance, growth, production and reproduction. Those nutrients need to be readily available and in the correct proportions of each to achieve the objectives.
There can be many consequences of excessive use of a certain ingredient just because it happens to be cheap at the time. An example would be to include very high level of high ash (minerals) meat and bone meal. High ash is an indication of lower protein quality due to higher inclusion of bones. You may fulfill the minimum required guarantees (maximum percent moisture, minimum percent protein, minimum percent fat, and maximum percent fiber) on your tag, but you need to realize that you are providing higher levels of calcium, phosphorus and other elements that will interfere with the utilization of some minerals and cause deficiencies. It may also impact the function of certain organs, such as the kidney.
Another example is the inclusion of an unusually high level of wheat by-product (wheat middlings). This ingredient (click here) can vary in its nutrients profile and may be used as a filler that provides some protein, phosphorus and fiber. A high inclusion rate may result in a bulky voluminous stool due to the undigested fiber. Its relative low energy level may dictate adding more fat to the kibble to meet the needed energy for growing, active dogs.
Trying to cut corners in the process itself can lead to unpleasant consequences such as losing a customer, ending sales or recalling the product if is proven to be unhealthy or unfit for sale. If a processor decides that he or she can do without a cooler for the kibbles prior to packaging, they may end up with mold growth in the bag. The combination of highly available nutrients in the extruded kibbles, heat, moisture and the presence of oxygen are ideal conditions for the growth of mold, yeast or bacteria. In other words, a recipe for ruining a quality processed product, simply because the processor failed to properly cool the end product.
To achieve success and stay profitable, there is no room for cutting corners. What you may perceive as cost reduction may turn out to be an expensive exercise in maintaining a profitable business.