Types of screw conveyor flighting
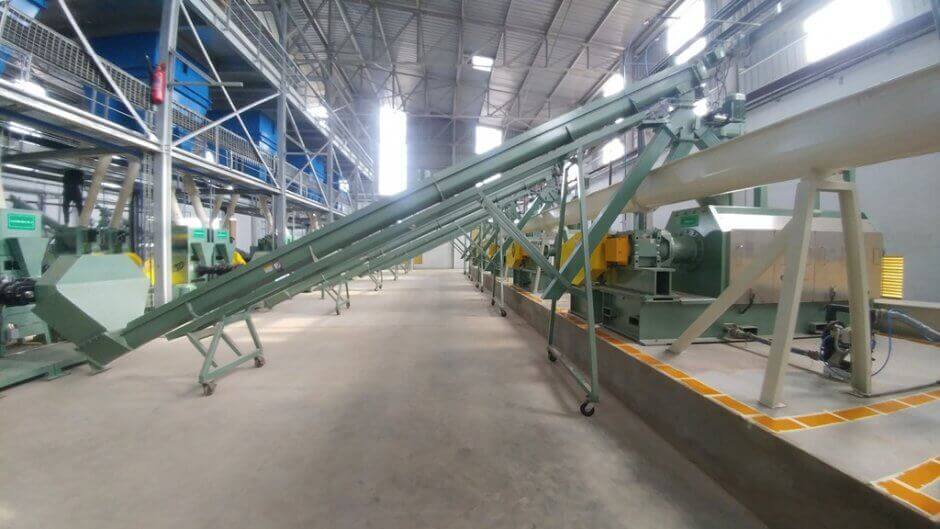
In our industry, the screw conveyor is a pretty common method of conveying. They’re simple, inexpensive and relatively universal. We tend to use a “U-trough” style of conveyor in our plants as do many other companies. A variation that you will see among these, however, is the type of screw/auger used inside of the trough. There are five to six variations, but today we’ll focus on three of them: regular/single, cut, and cut and fold.
Regular/Single flight
This is the most common type of profile. It’s used for bulk material flow and what you’ll commonly see in most feed mills. The flighting is continuous around the shaft of the screw. There are variations of this as well depending on application, but the most common is a standard pitch, single flight. This means that the screw diameter is equal to the pitch.
Cut flight
A slight variation of the single flight screw, a cut flight features small notches in the flighting where material has been removed from the profile. The purpose of this is to break up material during conveying, either for ease of material handling or preparation for the next process step. The flights tend to shred materials as they convey, which may or may not be desirable. The other thing to consider with this flight profile is that capacity is reduced as compared to a similarly sized single flight conveyor by a factor of 1.57x. As an example, a regular flight conveyor may be able to convey 9 tons/hour whereas a cut flight screw would convey 5.7 tons/hour.
Cut and fold
This is a slight variation of the cut flight screw. Rather than completely removing material from the flight, a small section is cut and folded out of the flight, creating a small arm. This acts like a paddle and works with the cut profile to break up and mix material during conveying. Cut and fold conveyors break up brittle materials very well and is what we recommend for conveying ExPress® cake to the cooler. The design promotes agitation by moving material from the bottom of the trough to the top, unlike a cut flight design. Material capacity is reduced with this design as well, this time by a factor of 3.0-3.5x. As an example, a regular flight conveyor carrying 9.0 tons/hour would carry 2.6-3.0 tons/hour as a cut and fold conveyor.
Selecting an appropriate profile will depend on the material transported and the process requirements. For us, we tend to use regular flights before pressing, then either cut flight or cut and fold depending on conveying distances and what the final processing steps will be. These will need to be appropriately sized as well due to the reduced capacity with each respective design.
Proper conveying is critical to the overall process. Our process engineering team will lay out the right equipment and conveying to optimize your facility.