Screw Elevators versus Bucket Elevators
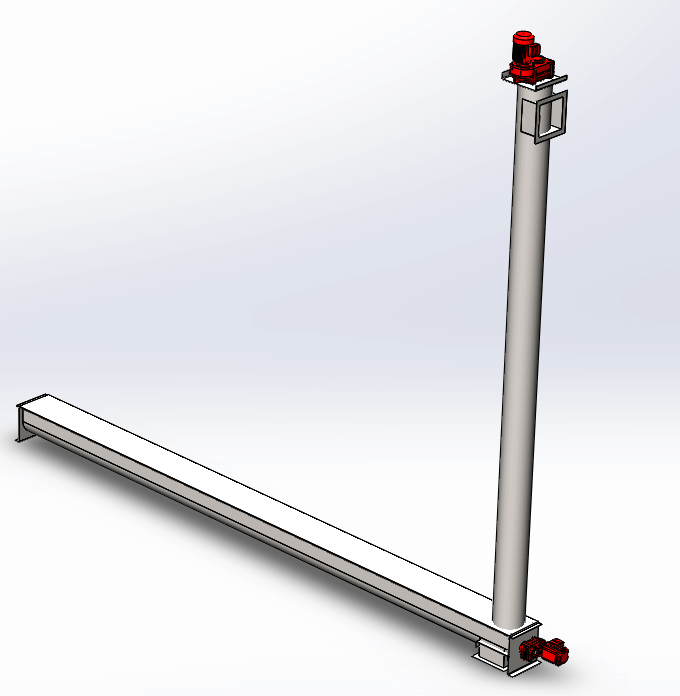
There are many ways to transport materials horizontally, but what if you need to go vertically? Pneumatics and cable-type methods are options, but the most common ones you’ll come across are screw elevators and bucket elevators.
Screw Elevators
A screw elevator is essentially two regular screw conveyors put together at a 90-degree angle. There is a horizontal portion and a vertical portion, each driven by its own motor. These are generally used when discharge clearance is an issue. For us, these are usually used to feed counterflow coolers as well as transport cooled meal from the cooler onto the next process step.
Screw elevators tend to be more expensive than bucket elevators, but maintenance is generally less since they have less moving parts and are easier to service. They are also better suited for high heat applications since the auger is made of steel.
Bucket Elevators
A bucket elevator is probably the most common way to convey material vertically. These can usually be seen on the outsides of feed mills with long spouts that are used to fill silos with material. Like the name suggests, there are a series of small buckets inside of the housing which attach to a long belt. This belt is wrapped around pulleys at the bottom and top, creating a large loop. Material is fed into an opening at the bottom of the elevator. As the buckets move with the belt, they scoop up the material from the bottom of the elevator, which is called the leg. The collected material rides along the belt and is thrown out of the top of the elevator, called a hood.
Bucket elevators tend to be less expensive than screw elevators, but with more moving parts and pieces, preventative maintenance is key for longevity. The belt and buckets will need to be tightened over time. Although not generally suited for high temperature applications, components can be specified for this if needed.
Which one?
When to use one versus the other comes down to application and personal preference. Larger capacities and taller discharge heights will primarily be situations for bucket elevators, especially in outdoor environments. Inside of a plant, however, there are pros and cons for each depending on the need and application.
When we work with customers on full plant designs, our Insta-Pro Engineering team will recommend the best solutions for our customer’s facility.